در دنیای ماشینآلات و صنایع سنگین نیروی هیدرولیک به عنوان یک شریان حیاتی عمل میکند. از بیلهای مکانیکی عظیم گرفته تا تجهیزات خطوط تولید پیشرفته سیستمهای هیدرولیک با انتقال سیالات تحت فشار امکان انجام کارهای فوقالعاده سنگین را فراهم میآورند. قلب تپنده این سیستمها شیلنگ هیدرولیک است؛ یک جزء حیاتی که وظیفه انتقال انرژی سیال را بر عهده دارد. اما سوال اساسی اینجاست: شیلنگ هیدرولیک برای چه فشاری طراحی شده است؟ درک مفهوم فشار طراحی عوامل موثر بر آن و اهمیت انتخاب صحیح شیلنگ نه تنها برای عملکرد بهینه بلکه برای ایمنی سیستمهای هیدرولیک نیز حیاتی است. این مقاله به بررسی جامع این موضوع از اصول اولیه فشار در سیستمهای هیدرولیک تا جزئیات فنی طراحی و کاربردهای مختلف شیلنگهای هیدرولیک میپردازد.
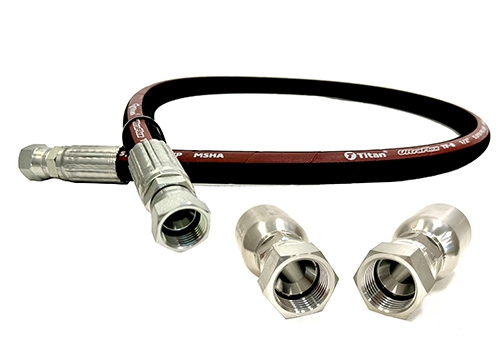
فشار در سیستمهای هیدرولیک: مبانی و اهمیت
سیستمهای هیدرولیک بر پایه اصل پاسکال عمل میکنند: “فشار وارد بر یک سیال محصور در تمام جهات به طور یکسان منتقل میشود.” این فشار که معمولاً بر حسب پوند بر اینچ مربع (psi) یا مگاپاسکال (MPa) اندازهگیری میشود نیروی محرکه لازم برای حرکت عملگرها (مانند سیلندرها و موتورها) را فراهم میکند.
اهمیت درک فشار در سیستمهای هیدرولیک از چندین جنبه قابل بررسی است:
- انتقال نیرو: فشار سیال هیدرولیک عامل اصلی انتقال نیرو از پمپ به عملگرها است. هرچه فشار بالاتر باشد نیروی بیشتری قابل انتقال است.
- عملکرد سیستم: محدوده فشار کاری سیستم مستقیماً بر سرعت قدرت و دقت عملکرد ماشینآلات تأثیر میگذارد.
- ایمنی: عدم انطباق شیلنگ با فشار کاری سیستم میتواند منجر به ترکیدگی شیلنگ نشت سیال و در نتیجه آسیب به تجهیزات محیط زیست و حتی اپراتور شود.
- طول عمر قطعات: انتخاب صحیح شیلنگ با توجه به فشار از فرسودگی زودرس و آسیب به سایر اجزای سیستم جلوگیری میکند.
اجزای اصلی شیلنگ هیدرولیک و نقش آنها در تحمل فشار
برای درک اینکه یک شیلنگ هیدرولیک چگونه فشار را تحمل میکند لازم است نگاهی به ساختار آن بیندازیم. شیلنگهای هیدرولیک مدرن معمولاً از سه یا چهار لایه اصلی تشکیل شدهاند که هر یک نقش مهمی در مقاومت فشاری ایفا میکنند:
-
لایه داخلی (Inner Tube): این لایه که مستقیماً با سیال هیدرولیک در تماس است معمولاً از لاستیک مصنوعی (مانند نیتریل نئوپرن یا EPDM) یا ترموپلاستیک ساخته میشود. وظیفه اصلی آن مقاومت در برابر سیال هیدرولیک (از نظر شیمیایی و دمایی) و جلوگیری از نشت است. این لایه باید صاف و بدون درز باشد تا جریان سیال را تسهیل کند و از تجمع ذرات جلوگیری کند.
-
لایههای تقویتی (Reinforcement Layers): این لایهها قلب ساختار مقاوم در برابر فشار شیلنگ هستند. آنها معمولاً از سیم فولادی بافته شده (Braided Wire) سیم فولادی مارپیچ (Spiral Wire) یا الیاف مصنوعی با استحکام بالا (مانند الیاف پلیاستر یا آرامید) ساخته میشوند.
- تقویت با سیم بافته شده: در این نوع سیمهای فولادی به صورت ضربدری و بافته شده در یک یا چند لایه روی لایه داخلی قرار میگیرند. این ساختار برای فشارهای متوسط تا بالا مناسب است و انعطافپذیری خوبی را ارائه میدهد.
- تقویت با سیم مارپیچ: در شیلنگهای با فشار بسیار بالا چندین لایه سیم فولادی به صورت مارپیچ و در جهات مخالف روی هم قرار میگیرند. این ساختار مقاومت فوقالعادهای در برابر فشارهای بالا ایجاد میکند اما انعطافپذیری شیلنگ را کمی کاهش میدهد.
- تقویت با الیاف: در کاربردهای با فشار پایینتر یا زمانی که نیاز به سبکی و انعطافپذیری بیشتر است (مانند برخی کاربردهای اتصالات پنوماتیک که فشار کمتری دارند) از الیاف مصنوعی استفاده میشود.
-
پوشش خارجی (Outer Cover): این لایه بیرونی معمولاً از لاستیک مصنوعی مقاوم در برابر سایش روغن آب و شرایط محیطی (مانند اشعه UV ازن و مواد شیمیایی) ساخته میشود. وظیفه آن محافظت از لایههای داخلی در برابر آسیبهای مکانیکی و عوامل محیطی است.
انواع فشار در مشخصات شیلنگ هیدرولیک
هنگام بررسی مشخصات یک شیلنگ هیدرولیک چندین نوع فشار مهم ذکر میشود که درک تفاوت آنها ضروری است:
-
فشار کاری (Working Pressure): این مهمترین پارامتر است و حداکثر فشاری را نشان میدهد که شیلنگ میتواند به طور مداوم و ایمن در شرایط عملیاتی عادی تحمل کند. این فشار همیشه باید از حداکثر فشار سیستم هیدرولیک بیشتر باشد. معمولاً برای افزایش ایمنی یک ضریب ایمنی (معمولاً 4:1) بین فشار کاری و فشار ترکیدگی در نظر گرفته میشود. به عنوان مثال اگر فشار کاری شیلنگ باشد فشار ترکیدگی آن حداقل خواهد بود.
-
فشار ترکیدگی (Burst Pressure): این حداکثر فشاری است که شیلنگ میتواند قبل از ترکیدن یا از کار افتادن کامل تحمل کند. همانطور که ذکر شد این فشار معمولاً چندین برابر (4 تا 5 برابر) فشار کاری است تا یک حاشیه ایمنی بالا فراهم شود.
-
فشار پالس (Impulse Pressure): در بسیاری از سیستمهای هیدرولیک فشار به طور مداوم نیست و دچار نوسانات ناگهانی یا “پالس” میشود (مانند فعال شدن ناگهانی شیرها یا تغییر جهت حرکت عملگرها). شیلنگ باید بتواند این نوسانات فشار را بدون آسیب دیدگی تحمل کند. تولیدکنندگان شیلنگها را برای تعداد مشخصی از چرخههای فشار پالس تست میکنند. این پارامتر برای کاربردهایی که با تغییرات فشار سریع و مکرر مواجه هستند حیاتی است.
-
فشار طراحی (Design Pressure): این فشاری است که سیستم هیدرولیک برای آن طراحی شده است. فشار کاری شیلنگ باید حداقل برابر با فشار طراحی سیستم یا کمی بیشتر از آن باشد تا ایمنی و طول عمر سیستم تضمین شود.
استانداردهای بینالمللی فشار شیلنگهای هیدرولیک
برای اطمینان از کیفیت قابلیت اطمینان و ایمنی شیلنگهای هیدرولیک بر اساس استانداردهای بینالمللی دقیق ساخته و آزمایش میشوند. مهمترین این استانداردها عبارتند از:
- SAE (Society of Automotive Engineers): این سازمان آمریکایی مجموعهای از استانداردهای دقیق (مانند SAE J517) را برای شیلنگهای هیدرولیک منتشر کرده است. این استانداردها الزامات مربوط به ابعاد مواد تحمل فشار مقاومت در برابر دما مقاومت در برابر سایش و روشهای تست را مشخص میکنند. انواع رایج شیلنگهای SAE شامل 100R1 تا 100R17 هستند که هر کدام برای سطوح فشار و انعطافپذیری متفاوتی طراحی شدهاند.
- DIN (Deutsches Institut für Normung): این سازمان آلمانی نیز استانداردهای مشابهی (مانند DIN EN 853 برای شیلنگهای بافته شده و DIN EN 856 برای شیلنگهای مارپیچ) را برای شیلنگهای هیدرولیک تعیین کرده است.
- ISO (International Organization for Standardization): ISO نیز استانداردهای بینالمللی را برای شیلنگهای هیدرولیک (مانند ISO 1436 برای شیلنگهای بافته شده و ISO 3862 برای شیلنگهای مارپیچ) ارائه میدهد که اغلب با استانداردهای SAE و DIN همپوشانی دارند.
هنگام انتخاب شیلنگ اطمینان از اینکه شیلنگ انتخابی با استاندارد مربوطه برای فشار کاری سیستم مطابقت دارد بسیار مهم است.
عوامل موثر بر فشار طراحی شیلنگ هیدرولیک
فشار نهایی که یک شیلنگ هیدرولیک میتواند تحمل کند تابعی از چندین عامل است:
- جنس لایههای تقویتی: همانطور که پیشتر ذکر شد سیم فولادی مارپیچ (چند لایه) مقاومت فشاری بسیار بیشتری نسبت به سیم بافته شده یا الیاف مصنوعی دارد.
- تعداد لایههای تقویتی: هرچه تعداد لایههای تقویتی بیشتر باشد (مثلاً 4 لایه سیم مارپیچ در مقابل 2 لایه سیم بافته شده) شیلنگ میتواند فشار بیشتری را تحمل کند.
- قطر داخلی (ID) شیلنگ: شیلنگهای با قطر داخلی کوچکتر (ID) معمولاً میتوانند فشار بالاتری را نسبت به شیلنگهای با ID بزرگتر تحمل کنند زیرا مساحت سطح داخلی کمتری برای فشار سیال وجود دارد.
- دمای کاری: دمای بالا میتواند بر خواص مکانیکی مواد شیلنگ تأثیر بگذارد و ظرفیت تحمل فشار را کاهش دهد. شیلنگها برای محدوده دمایی خاصی طراحی شدهاند و تجاوز از آن میتواند عمر شیلنگ را به شدت کاهش دهد.
- شعاع خمش (Bend Radius): خمش بیش از حد شیلنگ میتواند باعث تمرکز تنش در یک نقطه شده و مقاومت فشاری آن را کاهش دهد. هر شیلنگ دارای حداقل شعاع خمش مجاز است که باید رعایت شود.
- شرایط محیطی: قرار گرفتن در معرض مواد شیمیایی اشعه UV ازن و سایش مکانیکی میتواند به پوشش خارجی آسیب برساند و در بلندمدت بر یکپارچگی ساختاری شیلنگ تأثیر بگذارد.
- پالس فشار: نوسانات مکرر و شدید فشار (پالسها) میتوانند به خستگی مواد شیلنگ منجر شده و عمر آن را کاهش دهند. شیلنگهای طراحی شده برای کاربردهای با پالس بالا ساختار تقویت شدهتری دارند.
انتخاب صحیح شیلنگ هیدرولیک بر اساس فشار و کاربرد
انتخاب شیلنگ مناسب یک گام حیاتی برای ایمنی و کارایی سیستم هیدرولیک است. فرآیند انتخاب باید شامل مراحل زیر باشد:
- تعیین حداکثر فشار کاری سیستم: این اولین و مهمترین مرحله است. هم فشار ثابت و هم پیکهای فشار (پالسها) باید در نظر گرفته شوند.
- انتخاب شیلنگ با فشار کاری برابر یا بالاتر: هرگز شیلنگی را با فشار کاری کمتر از حداکثر فشار سیستم انتخاب نکنید. همیشه از یک حاشیه ایمنی استفاده کنید.
- بررسی محدوده دما: اطمینان حاصل کنید که شیلنگ انتخابی میتواند محدوده دمایی سیال و محیط را تحمل کند.
- سازگاری شیمیایی: لایه داخلی شیلنگ باید با سیال هیدرولیک مورد استفاده (روغن آب محلولهای دیگر) سازگار باشد.
- بررسی قطر داخلی (ID): قطر داخلی شیلنگ باید مناسب برای حجم جریان مورد نیاز سیستم باشد تا از افت فشار اضافی جلوگیری شود.
- انعطافپذیری و شعاع خمش: شیلنگ باید به اندازه کافی انعطافپذیر باشد تا در مسیرهای لازم نصب شود اما هرگز از حداقل شعاع خمش مجاز تجاوز نکنید.
- مقاومت در برابر سایش و محیط: اگر شیلنگ در معرض سایش یا عوامل محیطی خشن قرار دارد پوشش خارجی آن باید مقاوم باشد.
- نوع اتصالات هیدرولیک: انتخاب نوع صحیح اتصالات (مثلاً رزوه NPT JIC ORFS و …) و اطمینان از سازگاری کامل آنها با شیلنگ و پورتهای سیستم بسیار مهم است.
نقش اتصالات هیدرولیک در تحمل فشار
اتصالات هیدرولیک به اندازه خود شیلنگ در تحمل فشار سیستم حیاتی هستند. اتصالات نقاط اتصال شیلنگ به سایر اجزای سیستم (پمپ شیر سیلندر) هستند و باید بتوانند فشار سیال را بدون نشت یا خرابی تحمل کنند. ویژگیهای مهم در اتصالات:
- جنس: معمولاً از فولاد کربن (آبکاری شده) فولاد ضد زنگ یا برنج ساخته میشوند.
- طراحی و دقت ساخت: اتصالات باید به گونهای طراحی شوند که اتصال محکمی را با شیلنگ ایجاد کنند و از نشت در فشارهای بالا جلوگیری نمایند. تکنیکهای پرس کردن (crimping) یا مونتاژ (field attachable) باید با دقت انجام شوند.
- سازگاری با شیلنگ: هر نوع شیلنگ (SAE 100R1 100R2 و …) نیازمند نوع خاصی از اتصالات است که توسط سازنده شیلنگ توصیه میشود. عدم تطابق میتواند منجر به خرابی در فشارهای بالا شود.
- مقاومت در برابر لرزش و پالس: اتصالات باید بتوانند لرزشها و پالسهای فشار را بدون شل شدن یا آسیب دیدگی تحمل کنند.
تفاوت با اتصالات پنوماتیک
در حالی که هم سیستمهای هیدرولیک و هم پنوماتیک از سیالات برای انتقال نیرو استفاده میکنند تفاوتهای کلیدی در فشار کاری و در نتیجه در طراحی شیلنگها و اتصالات آنها وجود دارد.
- فشار کاری: سیستمهای هیدرولیک معمولاً در فشارهای بسیار بالاتر (صدها تا هزاران psi) کار میکنند در حالی که سیستمهای پنوماتیک از هوای فشرده با فشارهای نسبتاً پایینتر (معمولاً تا ) استفاده میکنند.
- سیال کاری: هیدرولیک از سیالات غیرقابل تراکم (مانند روغن) استفاده میکند در حالی که پنوماتیک از گازهای قابل تراکم (مانند هوا) بهره میبرد.
- طراحی شیلنگ و اتصالات: به دلیل تفاوت در فشار شیلنگهای هیدرولیک دارای لایههای تقویتی قویتر (سیم بافته یا مارپیچ) هستند و اتصالات آنها نیز برای تحمل نیروهای فشاری و کششی بالاتر طراحی شدهاند. در مقابل شیلنگها و اتصالات پنوماتیک معمولاً از مواد سبکتر (مانند نایلون پلیاورتان) ساخته میشوند و اتصالات اغلب از نوع فشاری (push-to-connect) هستند که برای فشارهای پایینتر مناسبترند.
طول عمر و نگهداری شیلنگهای هیدرولیک
حتی بهترین شیلنگ هیدرولیک نیز عمر محدودی دارد. عوامل متعددی میتوانند بر طول عمر آن تأثیر بگذارند:
- فشار کاری مداوم در نزدیکی حداکثر: اگر شیلنگ به طور مداوم در نزدیکی حداکثر فشار کاری خود عمل کند عمر آن کاهش مییابد.
- پالسهای فشار مکرر: پالسهای شدید و مکرر میتوانند به خستگی مواد منجر شوند.
- دمای بالا: قرار گرفتن طولانی مدت در معرض دماهای بالا به خصوص بالاتر از محدوده توصیه شده میتواند لاستیک را سفت و شکننده کند.
- خمش بیش از حد: نادیده گرفتن شعاع خمش مجاز باعث آسیب دیدگی داخلی شیلنگ میشود.
- سایش خارجی: سایش لایه بیرونی میتواند به لایههای تقویتی آسیب برساند.
- ناسازگاری سیال: استفاده از سیال هیدرولیک ناسازگار با لایه داخلی شیلنگ میتواند باعث تخریب شیمیایی آن شود.
- نصب نادرست: کشیدگی پیچ خوردگی یا خمیدگی نامناسب هنگام نصب میتواند عمر شیلنگ را به شدت کاهش دهد.
بازرسیهای منظم برای شناسایی علائم سایش ترکخوردگی برآمدگی نشت یا هر گونه آسیب دیگر حیاتی است. تعویض به موقع شیلنگهای آسیبدیده از خرابیهای ناگهانی و پرهزینه جلوگیری میکند.
نتیجهگیری:
پاسخ به سوال “شیلنگ هیدرولیک برای چه فشاری طراحی شده است؟” پیچیده است و به عوامل متعددی بستگی دارد. هیچ پاسخ واحدی برای همه شیلنگها وجود ندارد. هر شیلنگ هیدرولیک برای یک محدوده فشار کاری خاص طراحی شده است که توسط عواملی مانند جنس و تعداد لایههای تقویتی قطر داخلی دما و شرایط محیطی تعیین میشود. درک مفاهیم فشار کاری فشار ترکیدگی و فشار پالس همراه با رعایت استانداردهای بینالمللی مانند SAE و DIN برای انتخاب صحیح و ایمن شیلنگ هیدرولیک ضروری است.
همچنین انتخاب دقیق اتصالات هیدرولیک مناسب و اطمینان از نصب صحیح آنها به اندازه انتخاب خود شیلنگ حیاتی است. در نهایت با درک تفاوتهای کلیدی بین سیستمهای هیدرولیک و پنوماتیک به ویژه در مورد فشار و طراحی اتصالات پنوماتیک میتوان از انتخاب و کاربرد صحیح هر یک در جایگاه خود اطمینان حاصل کرد. ایمنی و کارایی در سیستمهای هیدرولیک تنها با انتخاب دقیق و نگهداری مناسب تمامی اجزا از جمله مهمترین آنها یعنی شیلنگ هیدرولیک تضمین میشود.